Rising tariffs, shifting U.S. trade policies, and a rapidly evolving industrial real estate landscape are challenging manufacturers across the country. At Hempitecture, we’re navigating tariffs by building long-term resilience through sustainable innovation and strategic flexibility.
Federal Funding Kickstarted Our Mission to Decarbonize
In 2024, Hempitecture was awarded over $8 million from the U.S. Department of Energy—a milestone that marked a new phase in our commitment to decarbonizing the built environment with plant-based, non-toxic insulation. But in today’s uncertain economic climate, federal funding alone isn’t enough. As tariffs on raw materials increase and government support fluctuates, the need for diversification and long-term strategic planning becomes essential.
How Tariffs Are Impacting U.S. Manufacturing—and What We’re Doing About It
Shifting trade policies are creating cost pressures for manufacturers, especially those dependent on imported materials or global supply chains. Hempitecture is actively navigating tariffs by:
- Investing in domestic agriculture by sourcing hemp fiber from American farms.
- Securing private capital to supplement government funding and maintain momentum.
- Expanding product offerings to enter new, sustainability-focused construction markets.
- Creating American manufacturing jobs that support rural communities and the clean economy transition.
This approach allows us to stay agile in the face of global and domestic policy changes—while advancing our mission to provide high-performance, carbon-negative building materials.
Supporting U.S. Agriculture and Blue-Collar Jobs
At the core of our strategy is a commitment to rural economic development. By sourcing hemp fiber locally, we reduce transportation emissions and support regenerative farming practices. At the same time, we’re scaling U.S.-based manufacturing facilities that create stable, green jobs in an era of industrial transition. This creates a resilient value chain: from field to fiber to finished product—all domestically grown and manufactured.
Industrial Real Estate: The Unsung Hero of Sustainable Manufacturing
Industrial real estate is more than just infrastructure. It’s a strategic lever for scaling climate-positive manufacturing. Read BOMA International’s (Building Owners & Managers Institute) coverage on Manufacturing Resilience.
Our facilities are purpose-built for processing and producing non-toxic insulation materials that meet modern energy and health standards. As regulations around indoor air quality and embodied carbon intensify, our operations are aligned with what the market—and the planet—demands. Facilities like ours are helping redefine what industrial real estate can be: flexible, efficient, and central to the new climate economy.
Responding to Demand for Healthier, Eco-Friendly Building Materials
Consumer preferences are shifting fast. Homeowners, builders, and developers are increasingly concerned with what’s behind their walls.
Hempitecture’s carbon-negative insulation meets this demand with:
- Non-toxic, plant-based composition
- Excellent thermal and acoustic performance
- Compatibility with modern green building certifications (LEED, WELL, etc.)
We’re seeing increased demand from industries focused on health, sustainability, and performance—especially in education, healthcare, and data infrastructure.
The Future of Industrial Real Estate: Smart, Sustainable, and Resilient
As technologies like AI, electric vehicles, and energy storage reshape the industrial sector, the need for sustainable, high-performance buildings is on the rise.
From data centers to advanced manufacturing hubs, tomorrow’s infrastructure requires:
- High-efficiency insulation
- Low-embodied carbon materials
- Resilient domestic supply chains
Tech giants like Microsoft are already prioritizing sustainability in their construction practices, and industrial real estate developers are following suit. Hempitecture is ready to meet this moment. Our carbon-negative products are built for the next generation of industrial growth—helping companies reduce their environmental impact while maintaining performance and cost-effectiveness.
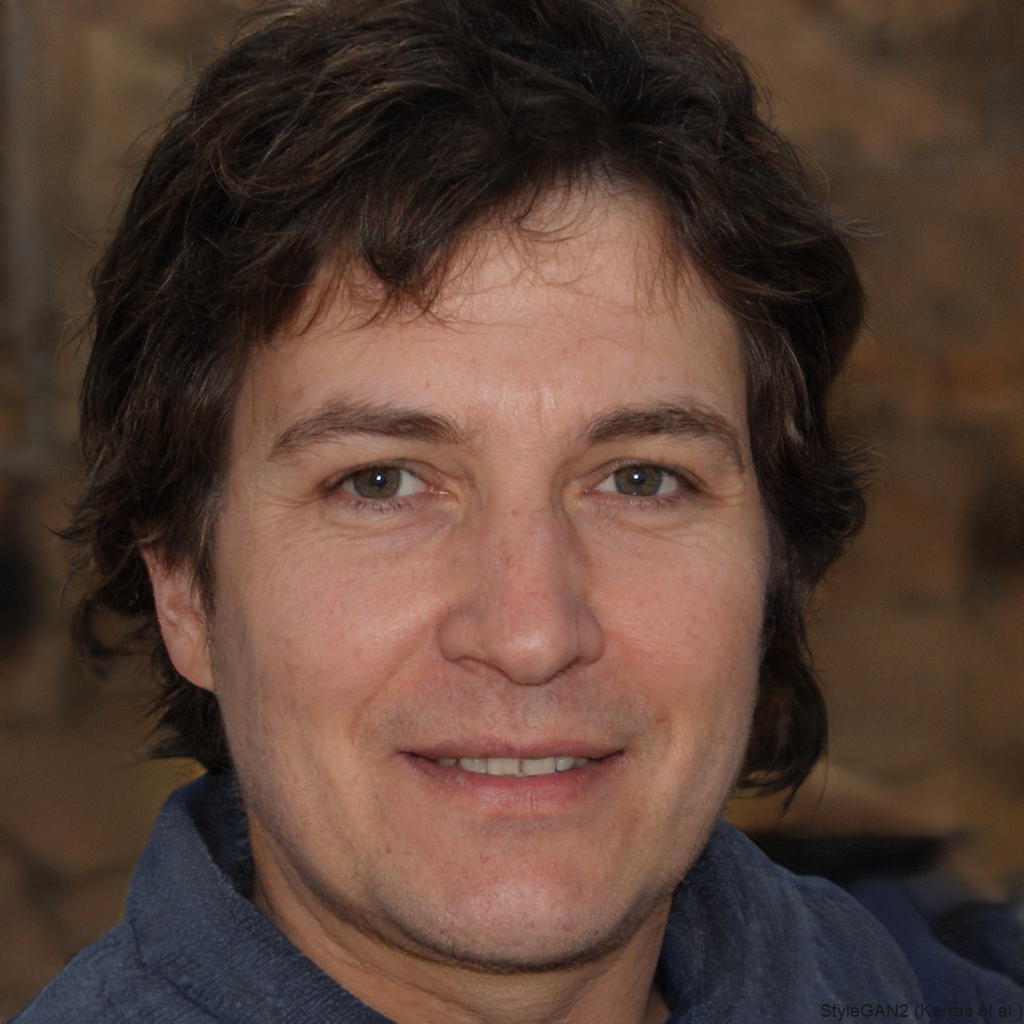
Mr. Roger Spataro offers a unique perspective on home improvement content, combining his writing skills with hands-on construction experience. Hailing from Chicago, Spataro began his career in the building construction industry after earning a Bachelor of Arts in English Literature from the University of Illinois at Chicago. He transitioned into writing, initially creating technical manuals and guides for construction professionals, allowing him to share his practical knowledge through the written word.